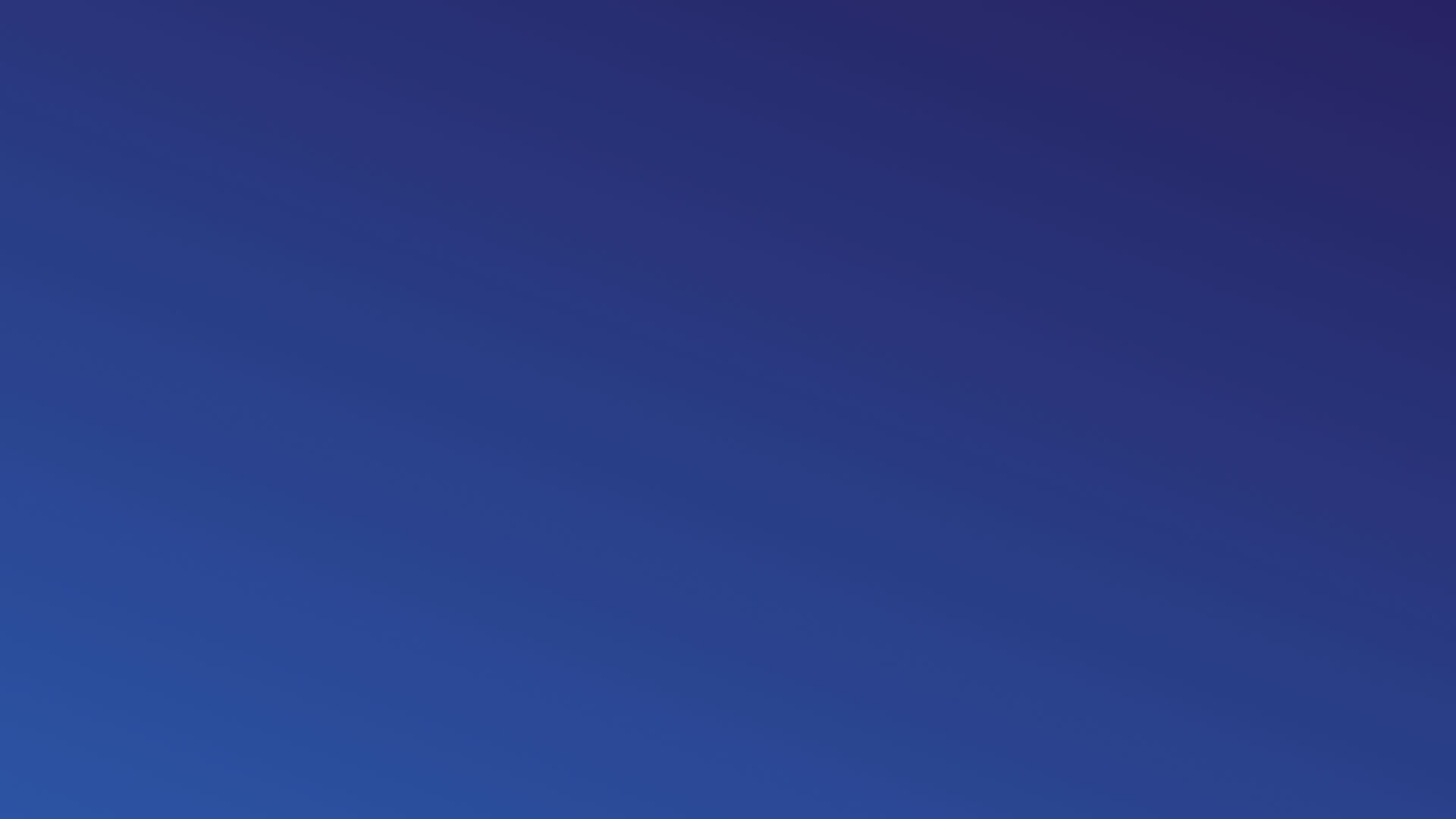



485x485x500 mm

Tool Racks

500°C - 3D Printing T°

200°C - Bed T°

150°C - Enclosure T°


ROBOTIC 5 AXIS

FILAMENTS & PELLETS

MULTI-MATERIALS

AUTOMATED

ADJUSTABLE

EVOLUTIONARY

THE
PERFECT
FIT
In order to succeed, the industry must shift towards printing ready-to-use functional parts with unrivaled performance in a highly productive manner.
​
Our innovative machine takes 3D printing a step forward by manufacturing functional parts without any compromise.
​
Our hybrid and ultra-functional printer allows you to manufacture complex, precise, functional and scalable parts in nearly any industrial-grade materials for a perfect fit rendering.
​
We automatized the process from end-to-end in order to provide a seamless experience that allows time efficiency, resource optimization, and industrial value.
SIMULTANEOUS ADDITIVE AND SUBTRACTIVE OPERATIONS
Printing and subtracting are carried out automatically, without the need for human intervention, resulting in post-processing operations layer by layer for precise, repeatable and high-quality surface finish parts.


ROBOTIC 5 AXIS MILLING
The 2 additional rotational axis allows you to post-process surfaces unreachable with traditional printers and remove the supports, for complex designs and ready-to-use parts.
FILAMENT AND
PELLET HEADS
Our 2 extrusion heads grant you access to pellet and filament materials but also enables the printing of bi-materials parts for an unlimited type of industrial parts.
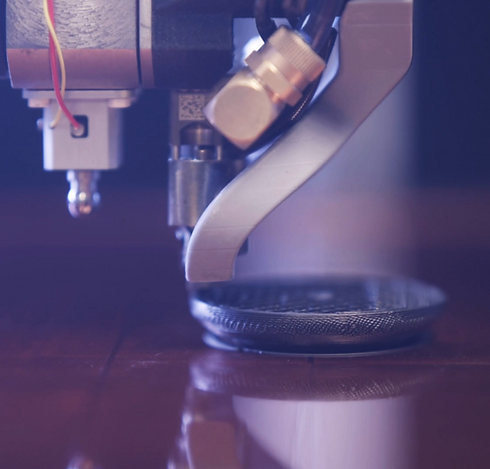

MULTIPLE
HIGH-PERFORMANCE
MATERIALS
4Shift supports 60+ materials empowering you to choose from a wide range of materials between polymers, composites, ceramics, and metals.
COHESIVE
BED SHEETS
Our different bed sheets ensure optimal adhesion of the first layer, whatever the material you want to print.


HIGH TEMPERATURE PRINTING
4SHIFT is able to extrude materials up to 500°C allowing the extrusion of high-performance materials and boosting printing speed.
AUTOMATED
TOOL CHANGER
The 4SHIFT's proprietary system allows additive and subtractive tools to be changed in seconds in a hands-free process for better condition control and resource optimization.


HEATED ENVIRONMENTAL PRINTING
The printing enclosure heats up to 150°C to decrease warping and layer delamination for better quality parts and increased mechanical properties.
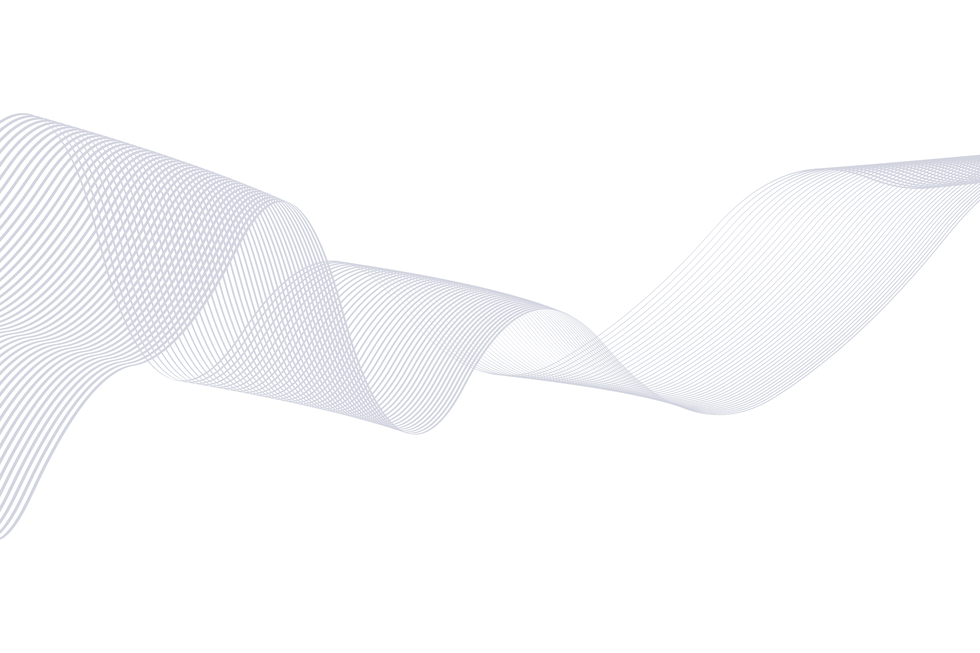
TECHNICAL SHEET
Bed surface
485 mm (L) x 485 mm (W) x 500 mm (H)
External dimensions
1800 mm (L) x 1400 mm (W) x 2625 mm (H)
Number of tool positions
4
Tooling changer
Automatic proprietary system
Calibration
True bed leveling
Reliability
Resuming process after power failure
End of filament detection
​
Nozzle size
from 0.2mm to 1.2mm
Granulometry
3,5 mm
Filament size
1,75 mm
Pellet tank capacity
7kg
Maximum milling speed
50k RPM
​
Thermic environment
Heating bed: maximum 200°C
Heated enclosure: maximum 150°C
Liquid tool cooling
​
​
Connectivity
Ethernet
Build area
Pneumatic bed suction
Choice of materials
Security
EEC certified
Filtration system (HEPA 13)
Door opening detection
General emergency stop
​
Control
22-inch touch screen
Computer and embedded software
Complete control interface
​
Software
Hybrid proprietary software
AN UNPRECEDENTED CHOICE OF MATERIALS


